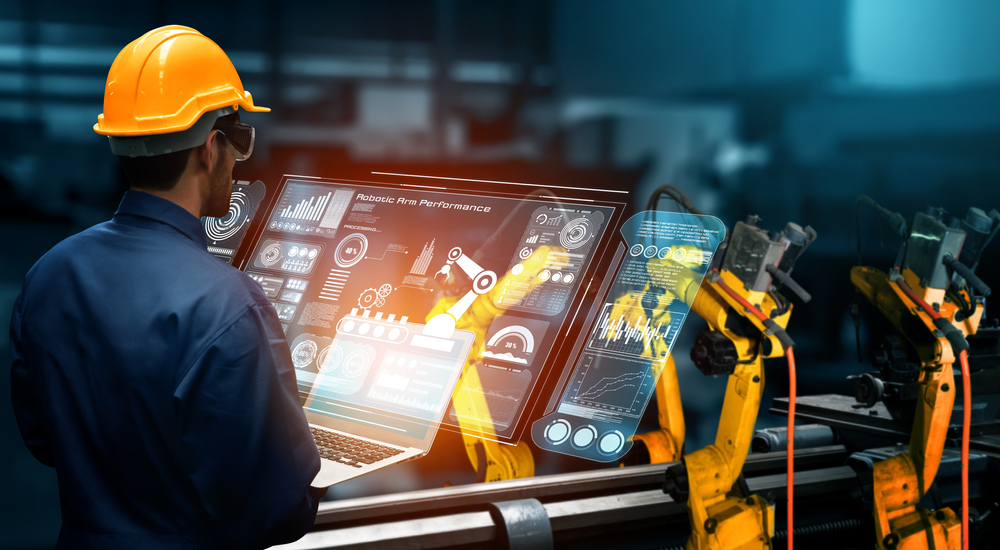
Sustainability is increasingly important to our customers around the globe, so in this article, we’ll uncover what we consider a “sustainable manufacturing plant,” why companies are pursuing sustainability, and the most common challenges along the way.
Moreover, the European Commission is currently working on a new proposal to make sustainable products a norm in the EU. And all companies will be expected to transform and comply in the next few years.
What is Sustainable Manufacturing?
Sustainable manufacturing is a mindset, first and foremost. At the moment, there’s no one globally approved definition of which activities are sustainable and which are not. To evaluate it, activities must be viewed and considered in the context of environmental, social, and governance aspects.
For example, it might not be sustainable to source lithium for battery manufacturing, but using e-scooters or e-bikes is part of solving the social challenge of more efficient transportation in the cities.
Sustainability in the manufacturing industry is considered a journey. It’s a way of thinking that helps strive toward reducing the negative impact on the environment and people.
Sustainable Manufacturing Process
In the context of manufacturing, a sustainable manufacturing process would in some way resemble how natural ecosystems work. A tree, for example, is consuming resources (nutrition from the soil, carbon dioxide, and sunlight) and is turning them into leaves, branches, and oxygen.
All the waste the tree has (e.g., leaves in the autumn) it throws on the ground where with the help of the natural ecosystem, turn into nutrition for the tree and other plants. As of now, we haven’t seen a manufacturing plant that would have managed to achieve this sort of process.
A manufacturing plant that uses waste to create new materials while running on wind and solar energy would be an example of a sustainable manufacturing plant. It uses materials in the local environment and creates a product through the production process.
The Competitive Advantage of a Sustainable Factory
The changing climate is already, directly and indirectly, impacting how we live and work and will increasingly continue to do that. Resources and energy prices are increasing and facing unseen before scarcity with no promise of change in this trend. This makes companies think about efficient and sustainable operations more than ever before.
For example, some of our clients are monitoring their energy consumption in real-time in relation to their production output to see how energy use can be made more efficient as waste is eliminated.
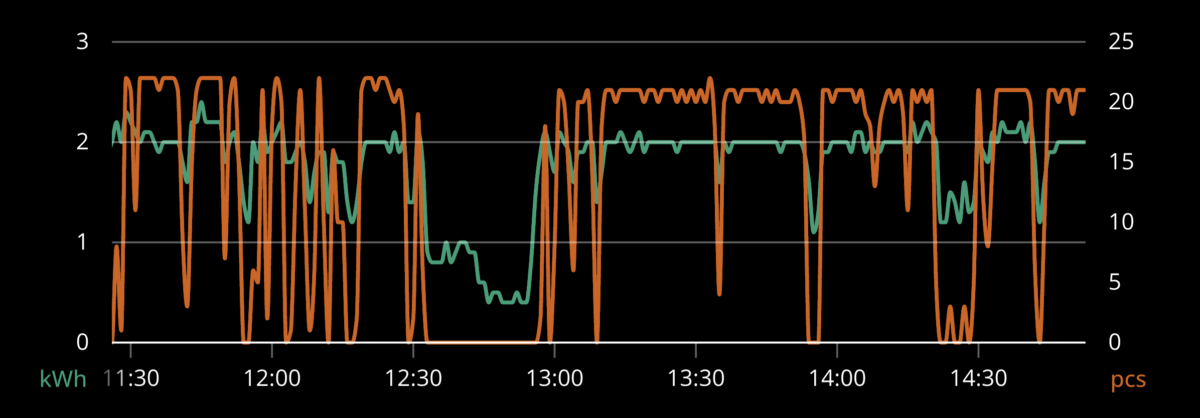
From a climate-related risk perspective, it’s clear – companies that understand their business risks from climate change can adequately prepare to mitigate them.
Some examples of risks businesses see due to change are:
revenue loss from customers hit by extreme weather events;
supply chain disruptions due to floods, droughts, fires, or heat waves;
carbon tax impact on the bottom line (source).
And these are just a few of them, as each business is in its unique situation. All this creates a very good business reason for remodeling factory floors and making them greener, more efficient, and sustainable.
In the article “10 Examples of Green Manufacturing Practices,” we’ve covered some of the steps that manufacturers can take towards sustainability.
To recap, solutions vary from case to case. Still, many are looking at ways to source materials from local suppliers, implementing more responsible sourcing of raw materials, or a plan for shifting to low-carbon operations.
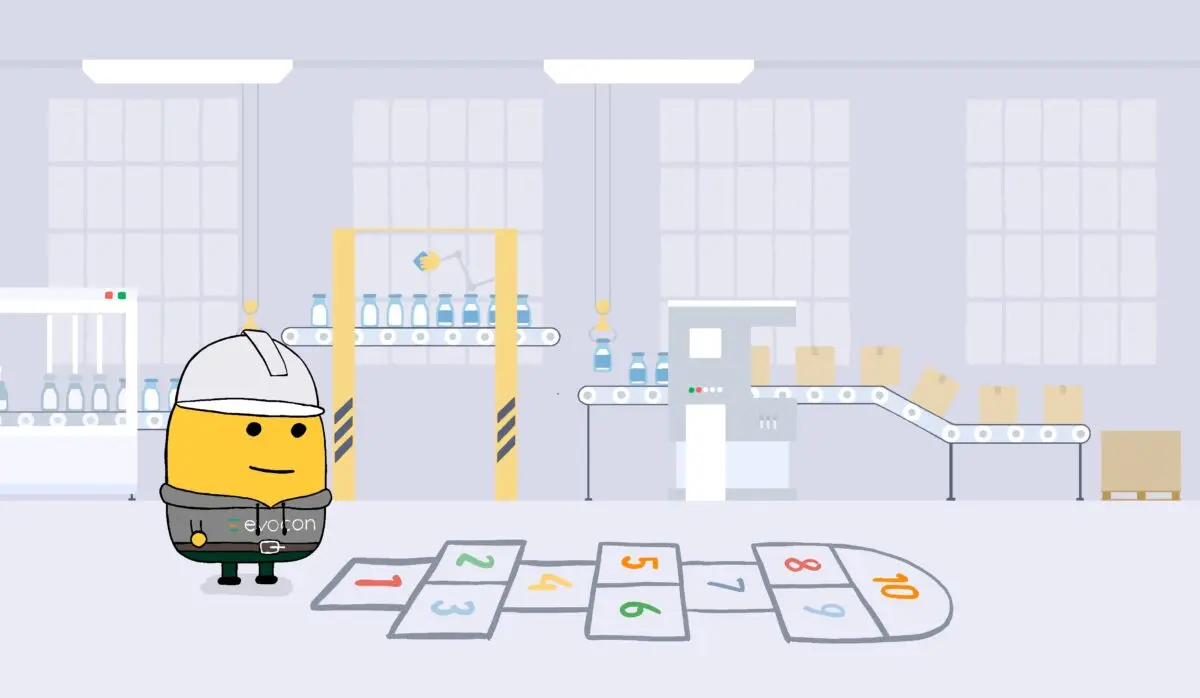
By the end of the day, a company running sustainable operations can weather the storm (literally) while competitors’ business is disrupted. Nonetheless, sustainable manufacturing practices can help save money and resources in the process.
Sustainable vs. Green Manufacturing
Most manufacturing companies can’t teleport from current business practices to a sustainable manufacturing process, so they often use “Green Manufacturing” as a guiding framework for improvements.
For example, Green Manufacturing is a bridge to get a company from inefficient non-renewable energy usage to reducing energy consumption and switching to a renewable energy source.
Evocon helps companies on the journey of eliminating material and energy waste by monitoring production in real-time and increasing OEE (overall equipment efficiency).
Challenges in Achieving Sustainable Manufacturing
As with any new initiative in the manufacturing industry, sustainability is faced with a fair amount of skepticism by many. One of the key issues with sustainability projects is that they require changing the current way of managing processes and require an initial investment.
In the 2014 report Profits With Purpose, McKinsey uncovers that almost half (48 percent) of survey participants admit that the pressure of short-term earnings performance is at odds with sustainability initiatives. This is still the case in many companies.
Finding a budget for projects that will pay off in, for example, 3 or 5 years is often hard to sell internally. That’s why sustainability initiatives must be considered a long-term investment to ensure the company has reduced business risks and increased profitability. And this has been proven repeatedly – companies that invest in ESG (environmental, social, and governance) outperform the competition. But the ROI often comes only in months or years (depending on the project).
Challenges in Achieving Sustainable Manufacturing
As with any new initiative in the manufacturing industry, sustainability is faced with a fair amount of skepticism by many. One of the key issues with sustainability projects is that they require changing the current way of managing processes and require an initial investment.
In the 2014 report Profits With Purpose, McKinsey uncovers that almost half (48 percent) of survey participants admit that the pressure of short-term earnings performance is at odds with sustainability initiatives. This is still the case in many companies.
Finding a budget for projects that will pay off in, for example, 3 or 5 years is often hard to sell internally. That’s why sustainability initiatives must be considered a long-term investment to ensure the company has reduced business risks and increased profitability. And this has been proven repeatedly – companies that invest in ESG (environmental, social, and governance) outperform the competition. But the ROI often comes only in months or years (depending on the project).
Examples of Companies on the Journey of Sustainable Manufacturing
As shared already at the start of the article, currently, there are no 100% sustainable manufacturers, but some examples in the industry can inspire us and show us what’s really possible. Let’s examine what makes Patagonia and Seventh Generation stand out
Patagonia
This is one of the most commonly used examples in the sustainability field. Why? They’ve achieved what many are striving for – sustainability is fully integrated into how they run their business:
they make products that last;
they repair the products that have worn down to extend their lifecycle;
they work with carefully selected suppliers that ensure safe, fair, legal, and humane working conditions;
majority of materials they use are organic, recycled, or natural;
they power their operations with renewable energy.
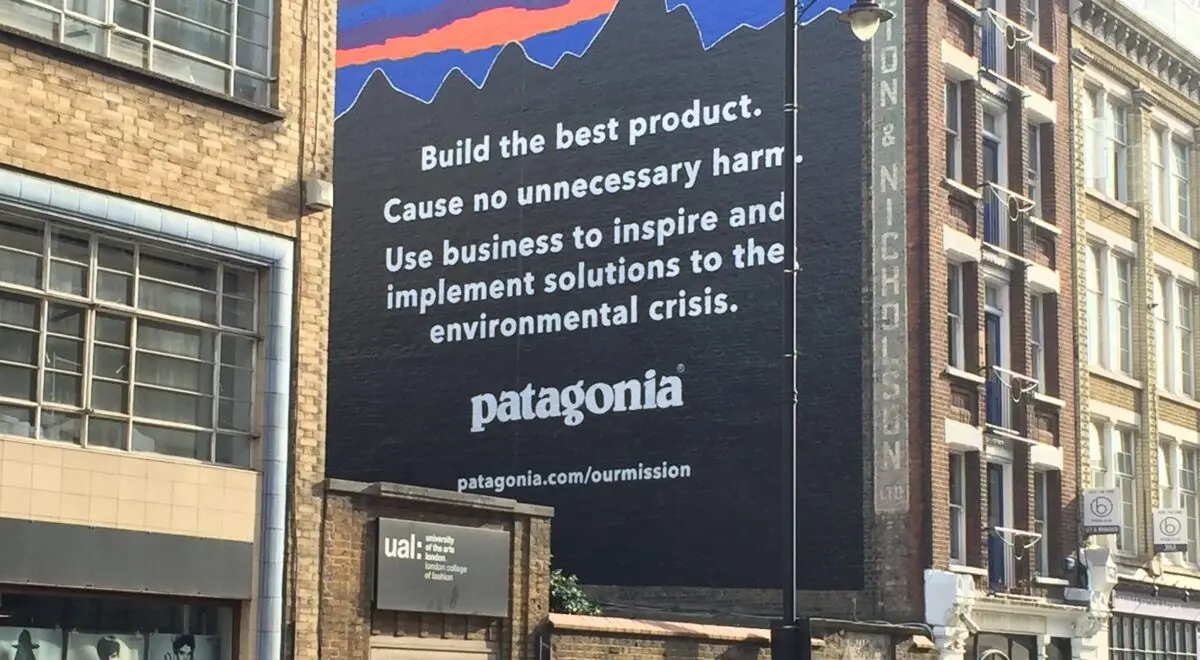
Seventh Generation
This company producing home cleaning supplies is revolutionizing the industry. They were the first homecare company to market unbleached, 100% recycled paper products in 1990 and have continued to lead the way for their competition. Since then, they’ve:
supported climate activism;
they stand up for paying a fair and livable wage to their employees and people in their supply chain who make product ingredients;
they’re working on completely eliminating chronic toxins from their products;
developed zero plastic packaging solutions.
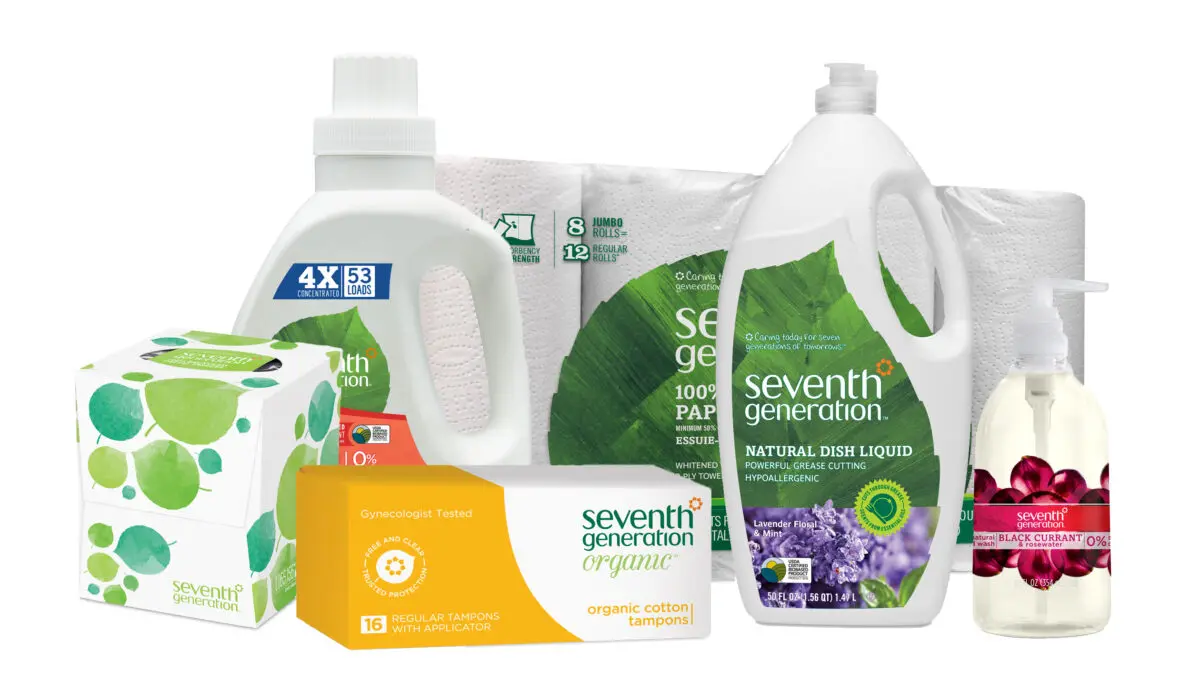
Take Your First Step Towards Sustainable Manufacturing
The initiatives the companies above spearhead are genuinely innovative and ahead of the industry. But don’t consider them impossible as every journey starts from the first step.
And we’re here to help our clients do exactly that. Your first step can be to:
reduce material wasted by improving quality;
get real-time data on production processes to improve energy efficiency;
reduce manufacturing carbon footprint by eliminating the Green Wastes.